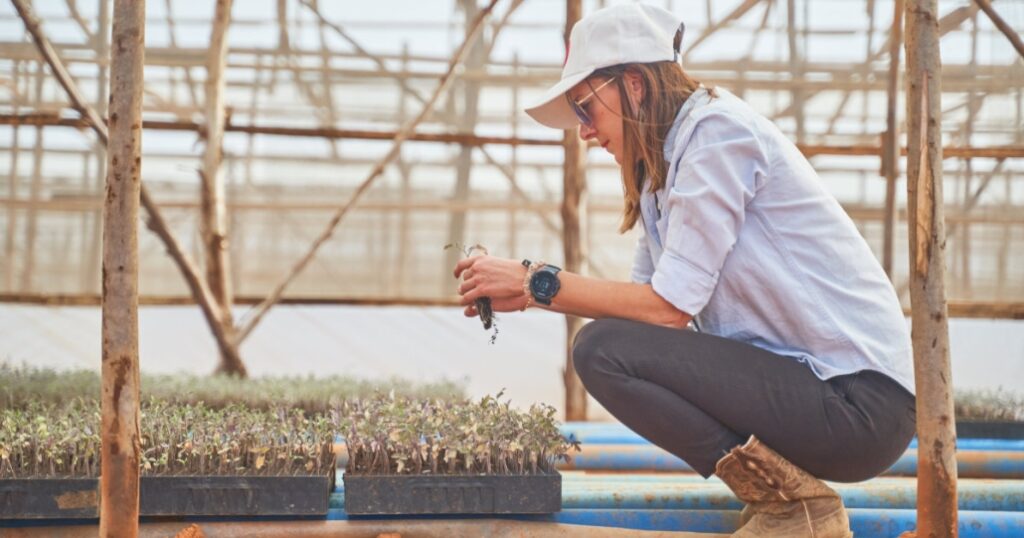
You may have heard of the jollof wars – which, for the unaware, is a passionate debate amongst West African countries as to which country’s jollof rice recipe is the best. Fundamental to the tastiness of jollof rice – and, indeed, many other foods consumed across the region – is tomatoes.
Nigeria, West Africa’s largest economy, has a stake in this culinary debate and, therefore, tomatoes: In response to the growing demand for tomatoes, farmers, particularly in the northern region of Nigeria, grow tomatoes as cash crops that are transported across the country and beyond.
Tomato has been a tender spot for Nigeria, with issues like storage, transport infrastructure, and disease affecting availability and crop yield. Over 1.5 million tons of tomato is harvested annually, however, most of this produce goes to waste. In fact, it is estimated that about 45% of fresh tomatoes harvested are wasted each year. With insufficient local production, importation has satisfied the growing local demand for many years. However, rising inflation, oil price volatility, and currency devaluations, amidst other macro factors have done little to mitigate the rising threats of food insecurity and farmers’ income.
Local production: the Tomato Jos factor
In 2020, tomato farmers in the small village of Kangimi in Kaduna state, Northern Nigeria, looked to the future with excitement and hope. An opportunity had landed on their doorstep: a new tomato processing plant was being built in their village. In the five years prior to the ground-breaking ceremony, the factory owners had supplied the farmers with farming inputs, techniques, and technology to increase tomato yields, then bought the fresh produce. This resulted in increased quality of tomato output, increased quantity of yield and income per farmer, and a strengthening of the tomato value chain.
That tomato processing factory, a $5 million project, was started in January 2020 mere weeks before a global pandemic was declared. By January 2021, a year after construction commenced, the factory was completed, making it the third largest tomato factory in Nigeria with the capacity to process 3.5 tons of fresh tomato per hour. It is also the only factory in the country to produce tomato paste without relying on imported concentrates. By mid-2022, products from the factory were already in the market.
The factory is owned by Tomato Jos, an agribusiness company founded by Mira Mehta in 2014. There are multiple implications of the factory operations: local production of tomatoes is increased ensuring economic productivity and wealth creation for rural communities around the factory, value chain for tomato is developed, throughput for manufacturing tomato paste is secured, quality made-in-Nigeria goods are produced, and the problem of food wastage – and, by extension, insecurity – is addressed.
As Aisha Mohammed, a small-holder farmer in Kangimi village, declared in a recent video that since she started working with Tomato Jos, “I have made tremendous progress in life. I paid my children’s school fees. I have capital to start a new business and I have built a house with the monies I made working for Tomato Jos company.”
According to Mehta in an interview with ThisDay newspaper, Tomato Jos currently has “over 200 full/contract workers, and a network of over 3,000 smallholder farmers who partner with the company to grow year-round at yields well above the national average.”
Understanding the local context
In building Tomato Jos, Mehta went on a learning journey on growing and processing tomatoes and agribusiness. Part of her research journey led her to California to talk with major growers and processors. However, Mehta notes the importance of understanding the local context whilst observing global trends: “You can’t just take a perfect system from California and plonk it down in Nigeria and expect it to work. You have to figure out which things move yield the most, and which things are possible in Nigeria given infrastructure constraints,” she said in an interview with the online platform, How We Made it in Africa.
With this perspective, Mehta and her team set about identifying the factors that led to the failure or underperformance of other tomato manufacturers in Nigeria. In doing this, they pioneered a new approach to tomato paste production and tapped into a business philosophy that other entrepreneurs in different sectors have identified: understand the local context and build the enabling pipeline, first.
For the first five years of the company’s life, Tomato Jos focused exclusively on farming thereby de-risking the upstream end of the business before investing in a factory. This approach to developing the upstream first before pivoting to manufacturing meant that the company understood the science and practice of growing tomatoes year-round (the approach also differentiated Tomato Jos from competitors who began with manufacturing before securing the upstream). So that when the factory was finally operational, Tomato Jos already had a sustainable pipeline for raw materials (tomatoes), avoided supply risks that may affect production, and had embedded infrastructures for distribution – including embracing digital technology and sustainable energy.
Like Lidya, Paga, and ReelFruit (all portfolio companies of Alitheia Capital), Tomato Jos took into cognisance the complexity of its business environment and paired this awareness with novel approaches to birth a production model that serves millions of people as producers, suppliers, distributors, and consumers.
In an interview with TechCabal, Tayo Oviosu, co-founder and CEO of the financial technology company, Paga, pointed out that his company, which began operation in 2012, followed a similar path: “The first couple of years of Paga was building infrastructure where it didn’t exist. We built a hybrid payment infrastructure for the online and offline customer.” Oviosu and the Paga team built for the local context by developing pipelines and infrastructures that enable further productivity.
Crucially, this approach also means that newer players have a template or roadmap to follow which translates to faster and more efficient deployment of innovations or solutions that have the capacity to unlock Africa’s full potential. Mehta and the Tomato Jos team, operating in a largely informal and underfunded sector, showed the potential for impact through innovative thinking and how patient capital can drive development.
TAGS: ALITHEIA CAPITAL, KANGIMI, TOMATO JOS, WEST AFRICA